If you’ve ever walked on a tile floor or scrubbed a tile shower wall, you’ve encountered grout as the cementitious mortar found within the seams of the tile pattern. However, recognizing where grout is used is only one step towards understanding this material. Proper grout preparation and application can mean the difference between creating a …
Grout vs Concrete: Differences Explained
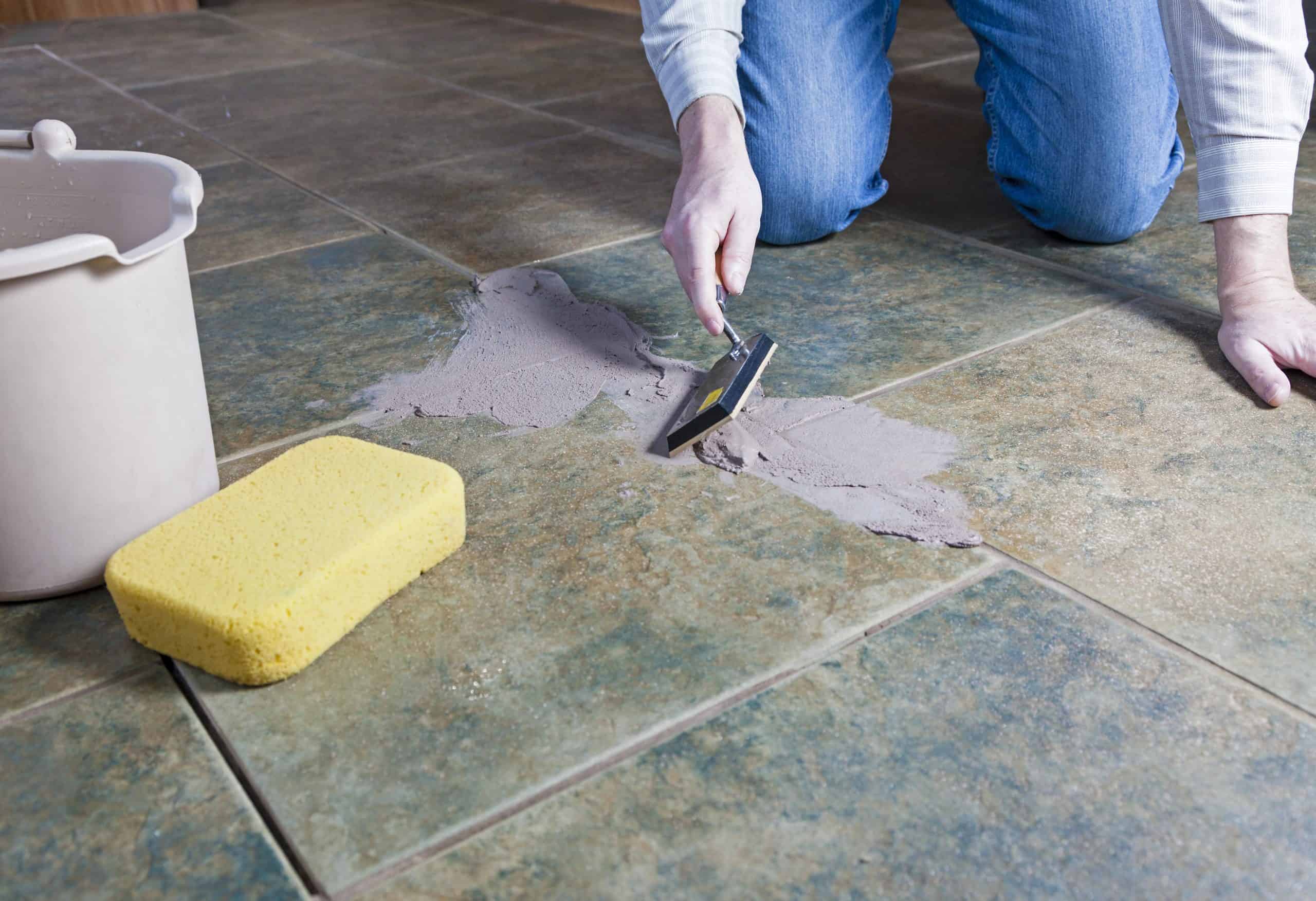
If you’ve ever walked on a tile floor or scrubbed a tile shower wall, you’ve encountered grout as the cementitious mortar found within the seams of the tile pattern. However, recognizing where grout is used is only one step towards understanding this material. Proper grout preparation and application can mean the difference between creating a beautiful water-tight barrier for your tile project or, alternatively, soaking through your sub-floor, concrete board, or drywall in areas where moisture is present on a regular basis.
What is Grout?
Grout is typically used to fill gaps and seams between tiles to provide water-, chemical-, and stain-resistant qualities to the tile work it is applied to. When mixed to the proper consistency, grout acts like a fluid and has a consistency similar to that of creamy peanut butter. Abiding by the chemical definition of a fluid, grout lacks rigidity and changes shape or flows when acted on by an external force. Liquids and gasses are also fluids. This is how grout is able to conform to and fill the small channels between tiles or line seams in stonework, no matter the width of each void.
Generally speaking, grout is composed of water, cement and, depending on whether the grout mixture is “sanded” or “unsanded”, sand. Grout mixtures also typically include plasticizers and pigments. Grout provides a finished look to tile, keeps debris out of the seams between tiles, strengthens the overall tile bond by providing rigidity to the area, and helps keep moisture from seeping under the tile.
Types of Grout
Sanded Cementitious Grout
As the name suggests, sanded grout mixtures contain sand in addition to Portland cement and water. This type of grout feels and looks gritty, thanks to the large silica sand particles incorporated throughout the mixture. These larger particles also provide a large amount of stabilizing surface area for the other ingredients to grab onto. This is why sanded grout is known to be highly resistant to cracking and shrinking.
Sanded grout is an excellent choice for larger grout seams thanks to its ability to resist cracking and shrinking. If the grout seam is 1/8th of an inch or larger, this type of grout is your best bet. Sanded grout is also the preferred choice for tile floors thanks to its stabilizing properties.
Due to its gritty texture, sanded grout is not the best option for fragile or highly polished tiles as it can scratch the surface of the tile during installation. It’s also not the best choice for very small grout lines due to the consistency of the sanded grout. It can be difficult to push sanded grout fully into thin seams of less than ⅛-inch. Because of this, installers sometimes thin their grout mixtures with additional water in order to fill these spaces more easily, but this is a bad idea.
Grout mixtures with too much water incorporated into the mixture can result in pinholes. These pinholes are caused by the evaporation of the excess water in the mixture.
Unsanded Cementitious Grout
Unsanded grout consists of Portland cement, polymers, pigments, and water. As you may have guessed, it contains no sand. As such, unsanded grout is not as strong as sanded grout, largely because the binding of the ingredients is done by the polymers and not by curing cement crystals grabbing onto countless sand particles as is the case with sanded grout. The lack of sand has its benefits, however.
Unsanded grout is very smooth and does not pose an etching threat to fragile, easily scratched tile or stone surfaces. It excels when used on thin tile seams of less than ⅛-inch. It is also extremely sticky which makes it an excellent choice for wall tiles.
Epoxy Grout
Epoxy grout is made from epoxy resins, pigments, and silica fillers. Many kits come in two parts, a resin and an activator. When set, epoxy grout is waterproof, crack-resistant, and shrink-proof. Additionally, it will not stain or discolor over time, and it does all of this without even needing to be sealed like its cementitious counterparts do.
Even so, epoxy grout can be more difficult to apply compared to either sanded or unsanded cementitious grouts, requiring much more prep time and cleaning before and after installation. It usually is not the best choice for porous tiles or stones as the epoxy can seep into these pores and change the look of the material by changing the texture or color or both. It is also three times more expensive than cementitious grout options.
Furan Resin Grout
Furan resin grout is made from a type of chemical alcohol called furfuryl and performs very similarly to epoxy grout. Kits come with two components: the resin is one component and an acid catalyst is the other component. One difference between epoxy and furan resin grouts is that furan resin grout is highly chemical and stain resistant, making it a top choice for industrial uses such as on flooring in laboratories, breweries, or commercial kitchens.
Concrete
Concrete is the most common building material in the world due to its strength, ease of installation, cost effectiveness, and versatility, and it’s one of the few materials that actually strengthens over time as opposed to weakening over time (when properly mixed and installed, of course). It is used to create slab foundations, basement walls, construction blocks, roads and road barriers. It is cast into architectural building elements and formed for use as supports and other structural components of large bridge structures. It’s even used to seal off radioactive waste. And these are only a handful of the many uses and applications of concrete.
What is Concrete?
Concrete consists of sand or gravel bonded together with water and cement which forms a fluid slurry that can be poured and formed into virtually any shape of any size and depth. This fluid then cures over time into a solid, stone-like composite material.
Types of Concrete
Because the ingredient lists for concrete are generally unchanging, the variability in common concrete types comes from only a few changeable characteristics of the mixture: strength (including tensile and compressive), density, and porosity. The most common concrete types are:
- “Plain” Concrete – This type of concrete consists of one part cement, 2 parts sand, and 4 parts aggregate (like gravel). It is used for things like pavement or other low-stakes construction projects that require little tensile strength.
- Lightweight Concrete – This type of concrete has a lower than typical density which is achieved by using low-density aggregate material in the place of gravel. Things like pumice, perlite, or expanded shale are used as the aggregate. Lightweight concrete is used in long-spanning or suspended structures like bridge decks.
- High Density Concrete – This type of concrete uses crushed barium as its aggregate. Barium has a density of 3.5 g/cm3, whereas pumice has a density of approximately 0.25 g/cm3. High density concrete is used for things like nuclear power plant construction and radioactive waste storage site construction due to its radiation-blocking capabilities.
- Rapid-Setting Concrete – This type of concrete has a higher percentage of cement than other concrete mixtures and contains additives that speed up the curing process. Because a slower cure time creates stronger concrete, and a faster cure time creates weaker concrete, rapid-setting concrete is typically used for things that are not intended to be strong structural components. It is commonly used for things like sidewalks, setting fence posts, and performing minor concrete repairs.
- Pervious Concrete – This type of concrete contains no sand and is composed of only cement and coarse aggregates. This composition allows for water to drain through porous concrete, making it an excellent choice for roadways and open pavement where stormwater absorption and runoff is a concern.
- Air-Entrained Concrete – This type of concrete is commonly used in freezing environments or where there is a substantial recurring freeze-thaw cycle and is made by adding foaming agents to the concrete mixture which, in turn, allows air pockets to be retained within the cured concrete structure. These air pockets allow for absorbed or existing water to expand when it freezes without damaging the concrete structure itself.
- Limecrete – This type of concrete is made using lime, sand, and aggregates rather than cement, sand, and aggregates. The aggregates differ slightly as well from typical concrete mixes. Instead of gravel, for example, limecrete uses lightweight aggregates such as glass fibers. This allows the mixture to be used in the construction of above-ground architectural shapes like domes and arches.
- Asphalt Concrete – This type of concrete is made from aggregates mixed with bitumen which acts as the binder. Asphalt concrete is used to pave roads, parking lots, driveways, airport runways, etc. It is the chosen material for these applications due to its permeability, skid resistance, durability, and its ability to expand and contract without becoming overly stressed easily.