The cost of epoxy flooring solutions can vary dramatically based on a number of factors. The most obvious cost driver is the type of epoxy used. Quartz-filled epoxy, for example, has quartz granules mixed into the resin product for added strength and texture. It's ideal for basements, laundry rooms, mudrooms, and storage spaces that …
The Cost of Epoxy Flooring Solutions- What You Need to Know
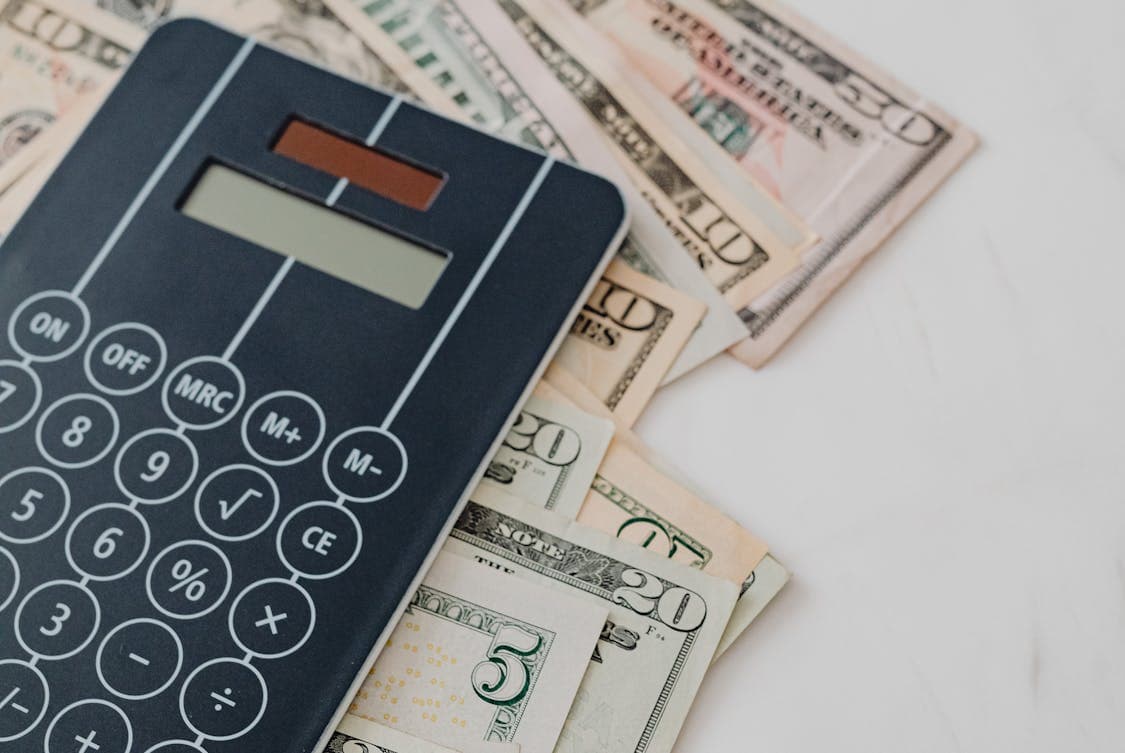
The cost of epoxy flooring solutions can vary dramatically based on a number of factors. The most obvious cost driver is the type of epoxy used.
Quartz-filled epoxy, for example, has quartz granules mixed into the resin product for added strength and texture. It’s ideal for basements, laundry rooms, mudrooms, and storage spaces that are prone to moisture.
Cost of Materials
The materials used to create epoxy flooring solutions can vary significantly. The type of material you choose will directly influence the cost, as well as any additional features you opt for. For example, the type of epoxy coating you select will affect how long it lasts and how durable it is. Solid epoxy offers a more durable finish than water-based or solvent-based epoxies, but it also tends to be more expensive.
Another factor that influences the cost of your epoxy floor is its thickness. Thicker applications offer greater protection and durability, but they also require more material and labor to apply. This is especially true if you opt for a 100% solid epoxy solution, which is typically reserved for industrial settings.
In addition to the type of coating, the concrete surface and prep process will also have a significant impact on the final price. For example, if your concrete surface needs to be repaired or leveled prior to applying the epoxy, this will increase the overall project costs. Additionally, if you choose to apply a primer or moisture barrier, this will also add to the total cost of your project.
A professional installation will generally cost more than a DIY kit, but it will save you time and money in the long run. A professional can provide a quick and mess-free application, as well as spot issues and perform any necessary repairs. Additionally, professional installations often come with warranties that will protect your investment. To make an informed decision about the best flooring solution for your garage or commercial area, take the time to discover quality flooring options for your space, as this will ensure durability, safety, and long-term value for your investment.
The final cost of your epoxy flooring will depend on the type and thickness of the coating, as well as any other options you select. For instance, a metallic epoxy system will typically cost more than a basic solid color option, but it will also offer a sleek and durable surface that is ideal for commercial or residential use.
While a DIY epoxy floor kit might seem like a great way to save money on your flooring project, it can be dangerous for the untrained eye. Mistakes during mixing, application, or curing can lead to a subpar result that isn’t as durable or as attractive as it could have been.
Cost of Labor
The cost of labor for epoxy flooring solutions varies depending on the type of floor you’re looking to create. For example, a retail space might require a more visually appealing coating than an industrial facility would, and this could increase the overall cost. Additionally, surface prep can also affect the total costs. For example, some epoxy coating products may need to be acid washed or etched in order to provide a clean surface for the final coat to bond with. This is essential for a long-lasting solution, and can add an extra $1 to $2 per square foot to the overall cost. Additional elements like non-slip additives or custom colors can also add to the cost.
When you’re considering epoxy flooring, it’s worth consulting a professional to help you decide what the best solution is for your space. They will have years of experience and will be able to guide you in selecting the right product for your needs. They can also help you prepare your existing concrete floors, which is crucial for the success of any epoxy floor. If the floor isn’t properly prepared, it can lead to ripples in the finished product, which will ruin its appearance and durability.
Additionally, professional installers will have access to high-quality materials that are often more durable and longer-lasting than those available to the general public. This is especially important for commercial spaces that need to withstand heavy foot traffic and equipment.
In addition, professional installers can save you time by working efficiently and completing the project in a shorter period of time. This can be beneficial for businesses that need to minimize downtime.
Finally, it’s important to consider any extra fees that might be associated with your installation. For instance, some companies may charge for a truck rental or moving expenses, and others might require you to empty your space before starting the job.
As you can see, the cost of epoxy flooring solutions varies widely depending on your specific needs. The best way to determine the exact cost of your project is to consult a professional who can assess your space and provide a detailed estimate. They will also be able to answer any questions you may have about the installation process.
Cost of Preparation
Many epoxy flooring solutions require the surface to be cleaned and prepped before the coating can be applied. This can be an extensive process and might include acid washing or etching to give the floor a “tooth” for the epoxy to bond with. This can add a significant amount to your overall cost, depending on how extensive the preparation is.
The type of coating you choose will also impact the price. Water-based epoxy is the most affordable option, while solvent-based epoxy costs more. Solid epoxy is the most expensive, but it’s also the most durable and resistant to chemicals and heat.
Labor is another major component of the cost of epoxy flooring. This includes surface preparation, application of the epoxy coating, and finishing touches. The amount of labor required varies from project to project, but on average, it accounts for up to 65% of the total cost.
It’s typically best to hire a professional contractor for installation of an epoxy floor, as they have the skills and tools necessary to ensure a high-quality finish. Moreover, they can often work quickly and efficiently to minimize downtime. Additionally, they will be able to recommend the best options based on your specific needs and goals.
Compared to traditional concrete floors, epoxy offers a more durable and visually appealing solution. It’s also highly versatile, with a wide range of colors, styles, and effects available. This versatility makes it a great choice for commercial and industrial spaces.
Epoxy floors are renowned for their long lifespan, and this longevity can translate to significant savings in maintenance costs over time. However, they can be tricky to maintain correctly, as improper care or cleaning can cause damage and premature failure.
Proper maintenance includes routine cleaning, prompt removal of spills, and avoidance of harsh chemicals. In addition, regular inspections can help to identify potential problems and prevent costly repairs.
Cost of Customization
The amount of customization used to create an epoxy floor can have a significant impact on the overall cost. Customization allows facilities to tailor the floor to their specific functional needs, while also adding a level of aesthetic beauty. This may include color, pattern, texture, or other features that improve safety or efficiency. While these options can add to the initial investment, they may also offer a high ROI in the long term.
The type of epoxy used in the floor can also affect cost. For instance, solvent-based epoxies are generally more expensive than water-based or 100% solids epoxy. However, the latter two options often have bonus features that make them a good choice for industrial floors. It is important to consult an expert to determine which type of epoxy will best suit your facility.
Another factor that influences the cost of an epoxy floor is the amount of preparation required. This can vary depending on the condition of the current floor and any repairs that need to be made. For example, if the floor has severe cracks or uneven areas, it will require more extensive preparation to ensure that the epoxy bonds properly with the existing concrete. This will add to the labor and material costs of the project.
In addition, the type of application method can also influence cost. For example, self-leveling epoxy can provide a more consistent finish and is more durable than other types of epoxy flooring. However, it is typically more expensive than other applications.
The size of the floor also has a direct impact on the total cost of an epoxy floor. This is because contractors usually charge by the square foot and a larger floor requires more materials and labor.
Choosing the right commercial or industrial floor is crucial to ensuring that your facility is safe and efficient. This is why it is best to leave the floor installation to professional contractors with experience in this field. These experts can help you choose the right type of epoxy flooring for your facility and ensure that it is installed correctly. This will save you time and money in the long run, as well as protect your investment by ensuring that the floor lasts for years to come.