Concrete projects, whether working on brand new or existing concrete, can sometimes feel like high-stakes chemistry experiments. The art of concrete is not a wholly complicated concept, but a multitude of factors can impact the overall appearance of your finished concrete, including moisture content of the mixture, weather conditions, curing conditions, porosity, and the overall …
Why Does Concrete Change Color? Reasons Explained
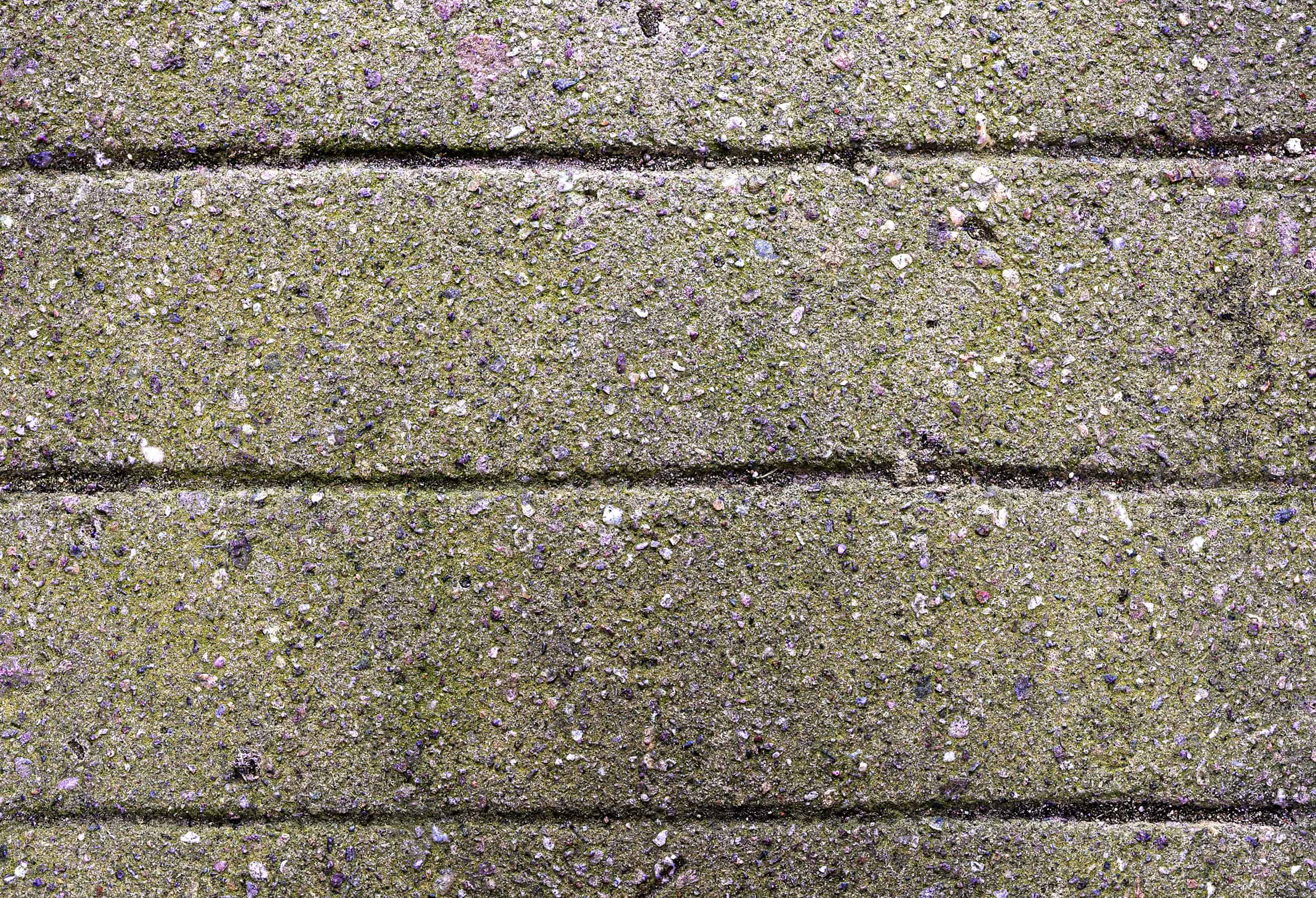
Concrete projects, whether working on brand new or existing concrete, can sometimes feel like high-stakes chemistry experiments.
The art of concrete is not a wholly complicated concept, but a multitude of factors can impact the overall appearance of your finished concrete, including moisture content of the mixture, weather conditions, curing conditions, porosity, and the overall composition of the mixture used.
The potential for variability between all of these factors can translate into inconsistent or unexpected color results for a new pour or concrete discoloration on existing work.
What do we mean by concrete discoloration and why does it occur?
The most common concrete discoloration issues observed are blotchy surfaces with variations between lighter and darker colors and white patches appearing on the surface of recently cured or long-existing concrete surfaces. The suspected causes and possible resolutions are shared, below.
Inconsistent or Blotchy Appearance (Darker Shades Mixed with Lighter Shades)
This form of concrete discoloration is usually a result of inconsistent water content, inconsistent mixing, inconsistent curing conditions, or poor workmanship. If you are not having your concrete mix delivered in one big batch and are mixing small batches and using them for the same project, you are much more likely to end up with a blotchy or inconsistent appearance. This is the case for a few reasons:
Inconsistent Water Content
The more water added to a concrete mix, the lighter it will be when it cures. If multiple batches are made and used on the same project, and even just a little more water is used in one batch versus another, you may experience both darker shades and lighter shades on the same concrete surface. To combat this, it’s important to precisely measure the ingredients for each batch and maintain the same moisture content between each.
A slightly more difficult task is to maintain the same prep-time and environmental conditions between each batch, as these variables can also impact how dry your concrete mix is when poured, thus creating color variations throughout your concrete. Your best bet is to use a consistent, single batch per project whenever possible.
Inconsistent Mixing
Concrete mixes often contain a compound called Calcium Chloride which accelerates the hydration of cement and speeds up the time it takes for concrete to set. However, if mixing is not consistent throughout each batch and between all batches, some areas of your pour will cure and dry slower than other areas, thereby creating both lighter and darker sections intermixed on the surface of a single concrete project. As with moisture content, it’s best to use one consistent, well mixed batch per project whenever possible.
Inconsistent Curing Conditions
There are basically two common types of curing concrete: wet curing and dry curing. Wet curing creates a much stronger concrete in comparison to dry curing because the water within the concrete mix evaporates much more slowly. Wet curing can mean spraying down the concrete multiple times per day, or it can mean covering the concrete with a polyethylene cover or a curing blanket.
Concrete discoloration can occur no matter which method of curing you choose for any number of reasons discussed in this article, but it all generally comes down to drying conditions and how consistent curing can be in terms of time, moisture, and temperature.
One example of this variability being possible (even when consistency is strived for) comes from using a polyethylene cover during a wet cure and still experiencing concrete discoloration due to something called the “greenhouse effect”. As moisture evaporates at the surface of the concrete, wrinkles in the cover can unevenly capture moisture. The moisture then condenses and drips back onto the surface of the concrete inconsistently, thus allowing the concrete to dry unevenly and creating a blotchy appearance in the finished concrete.
Variability in the weather can cause inconsistencies in concrete coloring as well. For example, it can rain during an uncovered cure, it can be very hot outside and one part of the concrete can be in the shade while the other is not, it can be very windy and whisk away moisture from the surface unevenly, etc.
In order to combat concrete discoloration, the goal should always be consistency throughout mixing, pouring, troweling, and curing during a concrete project. It is also beneficial to use a curing compound to assist in maintaining consistency, as these products create an even, protective film that prevents water from evaporating too rapidly. Some even perform double duty and act as a sealer while also acting as a curing compound.
Poor Workmanship
Concrete discoloration isn’t only caused by environmental factors like mixing consistency and evaporation speed. It can also be caused by the person performing the work. Trowel burning is a common issue that results in dark patches of concrete as a result of hard-troweling to the point that the concrete is made more dense as the water content is reduced by effectively pushing water from the trowel-burned area to non-trowel burned areas. This generally occurs when the surface is so stiff that the trowel can be held at a greater angle without affecting the overall surface texture. The increase in angle also increases the pressure of the trowel on the underlying material. To avoid this issue, avoid increasing your trowel angle and maintain consistent troweling pressure throughout your project.
Patches of White Minerals on a Concrete Surface
This form of concrete discoloration is typically due to a process called efflorescence, which is defined loosely as the movement of salts through porous material. There are two forms of efflorescence that can change the appearance of concrete: primary and secondary. Each of these can impact concrete at different times and in different ways.
Efflorescence, Explained
In order to help you visualize the process of efflorescence, consider a recently poured, not yet fully cured, and unsealed slab of concrete that has been placed or formed on moist ground.
Because concrete is a very porous substance, it contains small pockets of void space in between and throughout the entire material structure. These pockets provide excellent pathways for water and water-soluble minerals, including salts, to migrate upwards towards the surface. At the surface, the water eventually evaporates, and the salts that were dissolved in the water are left behind, no longer dissolved and causing white patches of discoloration that can sometimes be difficult to remove.
Primary efflorescence occurs during curing and does not incorporate any type of chemical reaction to the concrete or the additives added to the mixture, itself. Rather, this process simply deposits salts onto the surface of the concrete that are already present within the concrete mixture, thereby changing the color of the concrete surface while not impacting the overall structure in any way.
Secondary efflorescence occurs when an external water source, like rain or snow, comes into contact with the concrete which then absorbs the water and water-soluble salts that were not a part of the original concrete mix. An example of this is when road salt mixes with snow and melts in a parking garage. This type of efflorescence has the potential to structurally alter the concrete by slowly dissolving components of it while also causing discoloration, and is, therefore, of arguably greater concern than primary efflorescence.
How to Prevent or Remove Discoloration Caused by Efflorescence?
If you did not choose any additives to prevent efflorescence and your concrete has already been poured, you might begin to notice white patches of salt on the surface of your concrete as the concrete cures. The trick is to remove the deposits as you notice them and before they solidify or react with the concrete surface. If you can manage that, all you may need to do is brush off or rinse away the deposits with a pressurized washer. However, without additional modification, these white patches may continue to appear intermittently and will need to be cleaned each time in order to prevent them from requiring more extensive removal efforts over time, like acid washing or grinding.
If you find that you are unable to brush or wash away the white patches, you can try washing the efflorescence away with diluted vinegar (for a more natural solution) or a cleaning product specifically designed to remove efflorescence without the over-use of acids that can make the problem worse, or you can use an acid like hydrochloric or phosphoric acid. Keep in mind that if you use a strong acid to remove efflorescence, you will need to neutralize it with a mild base and rinse thoroughly with water so as not to damage your concrete. If this still does not work, try grinding off the efflorescence with a concrete grinder.
However, it is much more beneficial to prevent primary efflorescence in the first place rather than attempting to solve the problem later on. One such preventative would be to use admixtures capable of transforming salts into other non-leachable, non-migrating chemicals anytime water is present.
Another option is to place a barrier between other materials and the concrete in order to prevent the uptake of water and water-soluble salts, something called a capillary break. Capillary breaks can be in the form of a membrane or a liquid.
A third option is to use a deeply-penetrating, impregnating, hydrophobic sealer which works by repelling water, thereby preventing water-soluble salts from penetrating the concrete from above or below.
Colorful Concrete Discoloration (Blue, Green, Orange, or Red)
Blue or Green Discoloration
A common component of concrete is slag cement which works together with Portland cement to strengthen concrete by reducing its porosity, inhibiting the corrosion of rebar, and increasing its overall resistance to a common internal concrete phenomenon called “chemical attack”. However, the iron sulfides and ferrous oxides present in slag cement can cause blue and green discoloration in concrete, especially those pieces poured into non-lumber forms.
This type of concrete discoloration is caused by incomplete chemical reactions between the slag cement, Portland cement, and oxygen in the air, and is often observed in concrete that is poured into large forms with coated or non-porous surfaces, like melamine plywood or steel. This is because these kinds of forms allow much less air into the form than lumber does and the degree of discoloration is increased when less air is able to reach the concrete.
This kind of discoloration can be prevented by using lumber forms or by loosening or opening the forms as soon as feasible after pouring and setting, but discoloration can be improved after the fact with time and air exposure. Highly oxygenating substances can also help remove this kind of discoloration, such as hydrogen peroxide, when applied directly to the affected concrete.
Orange or Red Discoloration
Orange and red shades are additional variations of concrete discoloration. However, rather than occurring due to any aspect of the formation of the concrete, this type of discoloration generally occurs on existing concrete and is caused by frequent contact with water that either has a high iron content or is caused by oxidized iron-containing (rusted) metals being in close contact with the concrete, especially after continuous contact with water.
An acid-based cleaner can assist in removal of rust stains from concrete, whether a professional-grade product or a common household acid, like vinegar, lemon juice, or soda.